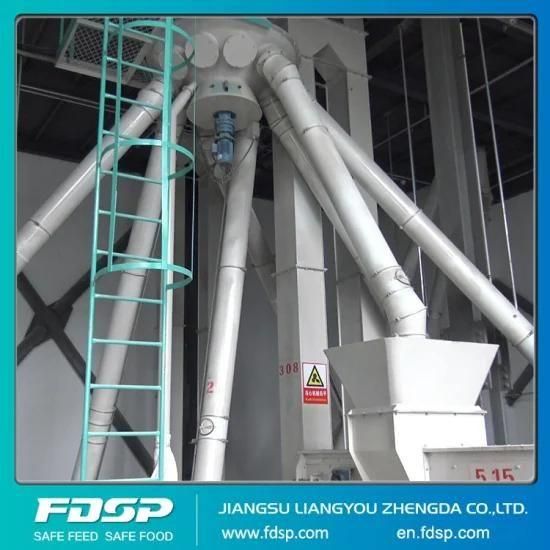
Case Analyse 80tph Corn Deep Processing Production Line
Jiangsu Liangyou Zhengda Co., Ltd.- Port:Shanghai, China
- Production Capacity:80sets Per Year
- Payment Terms:L/C, T/T, D/P, Western Union, Paypal, Money Gram
- After-sales Service:Engineer Available
- Type:Pellet Mill
- Processing Object:Cereals
- Processing Technics:Crushing-before-Mixing
- Screen Mesh:With Screen Mesh
- Grinding Equipment Type:Feed Hammer Mill
Base Info
- Model NO.:FDSP series
- Pellet Mill Type:Ring Die Pelleter
- Bulking Machine Type:Twin Screw Bulking Machine
- Expanding Method:Wet Expansion
- Condition:New
- Applicable Materials Shape:Granular
- Warranty:1 Year
- Trademark:FDSP
- Transport Package:Pallet
- Specification:set
- Origin:Jiangsu China
- HS Code:843610000
Description
TECHNICAL PART
Brief introduction for flow process
It is designed to produce 80t/h, using three grinding lines, two mixing lines, one pelleting line and four packing lines.The total power of the equipment is about 1300KW.The construction area of the production zone is about 22×18×31.5m, allocated with 1.5T boiler.The whole line is compact in design, reasonable in structure, meets the environmental protection requirement, and can carry on the directional design according to the customer request.
Technological process chart:
RM Receiving & Precleaning System-Grinding System-Dosing & Mixing System-Pelleting System-Bagging System-Auxiliary System
Technological characteristics and introductions:
RM receiving and cleaning process: Granule material is dumped and cleaned, individually dust collected which is with the better effects.

Grinding process: 3 sets of hammer mill is adopted in this process, 2 grindings bins are equipped for each hammer mill to crush different raw material at the same time which improves the productivity; The impurities could be removed from raw material by magnetic separation equipment before grinding bins to ensure the safe running of hammer mill.
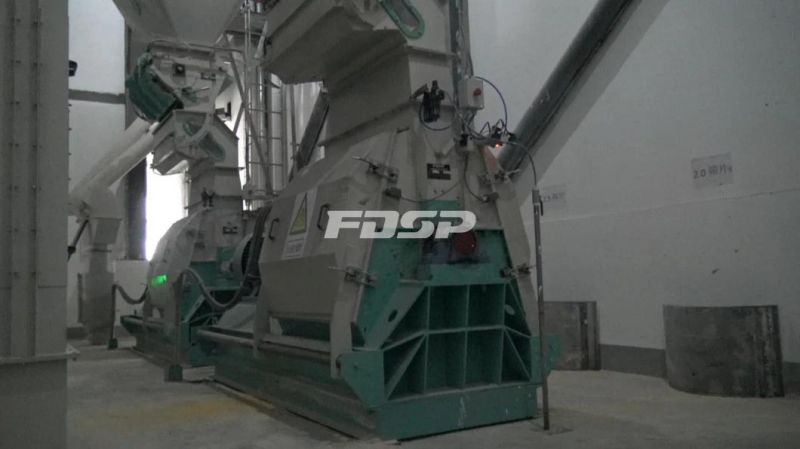
Batching and mixing process: in this process, we use 18pcs batching bins, two batching and mixing systems are allocated. Each batching system is allocated with 1 batching scale to work at same time, which is controlled by FDSP developed independently batching program, achieve accurate quick and slow feeding, quick batching and with high accuracy.

Mixing equipment( 2sets): SHSJ6, (45KW,3000kg/batch), designed output 35-45t/h/set, homogeneity CV≤5%.
Pelleting process: one set double-layer conditioner pellet mill is used in this process. Two pellet bins are equipped for the pellet mill, which is easy to sift when replacing the varieties. After pelleting, the pellets enter into the cooler, bucket elevator and then go to screening by rotary screener. The finished products go to the packing bins, others screened powder material goes back to the pellet mill.
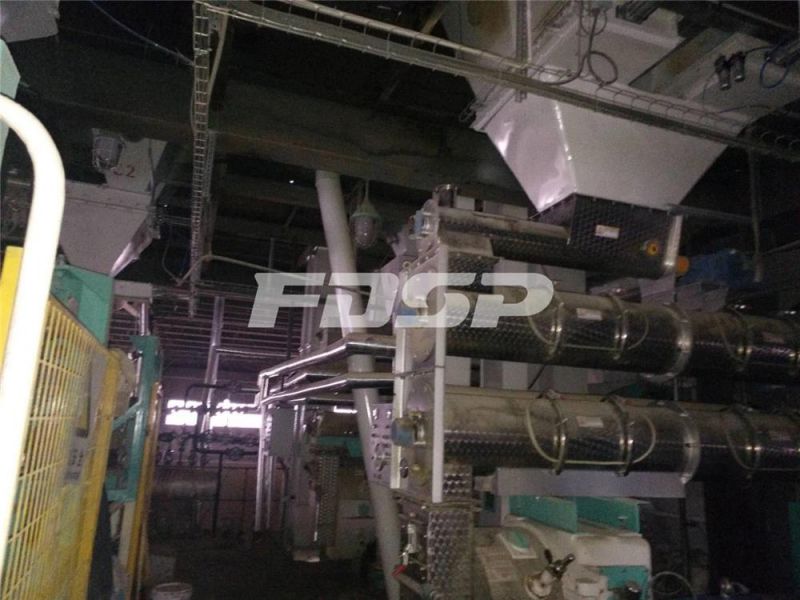
Cooling equipment( 1set): SKLN10,output 20-25T/H.
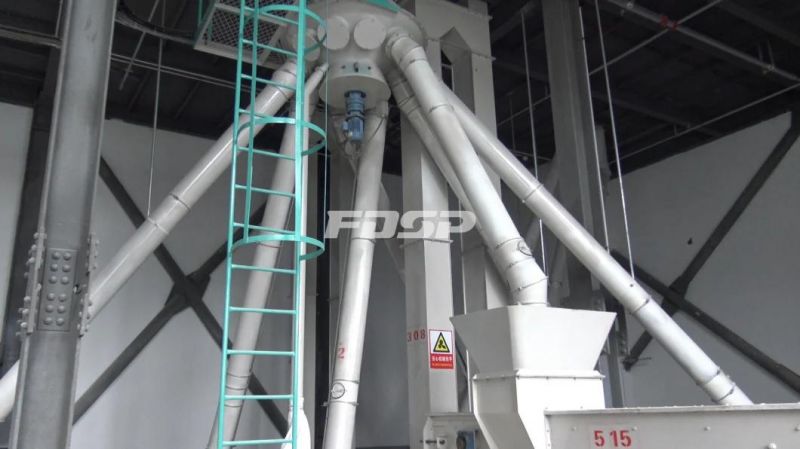
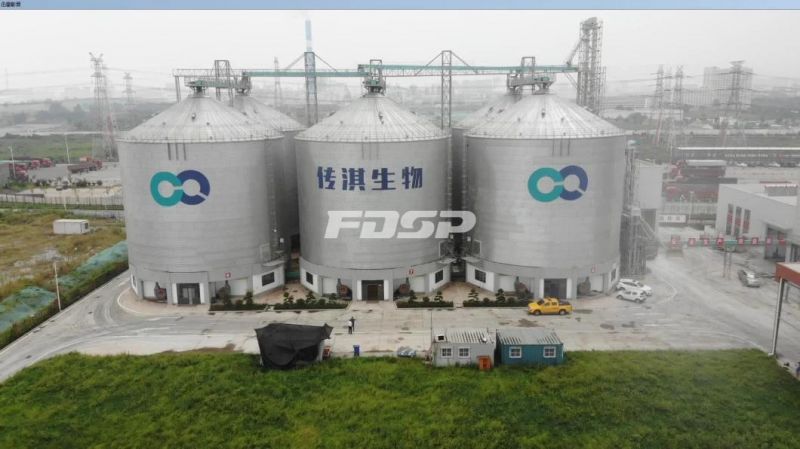
Packing process: There are 4 FP bins in this process, 2 of them can store both mash feed and pellet feed. There is special anti-grading device for mash feed bins. The pellet feed and mash feed will be weighed and packed finally by packing scale. 16 bulk bins are designed for bulk trucks shipping at the same time.
Packing equipment: Ton packing scale(both for mesh feed and pellet feed), weighing rage 800-1000kg/bag, 6-10bags /min.
The process can be optimized according to different customer needs:
1. Single point dust collection mode is used in the plan which means pulse filter is equipped for every rotary distributor(mesh) and granule cleaner with good effect. Single point dust collectioniskind of humanized design of our company, to provide a better working environment, but the cost increases, customers can consider whether it is needed in actual situation;
2. The quantity of bins can be adjusted to achieve the beast use ratio and effectively control the production cost based on factors such as customers' formula, characteristics of raw materials.
3. The dust removal design at bagging process can improve the working environment of workers, and customers can configure it according to their needs.